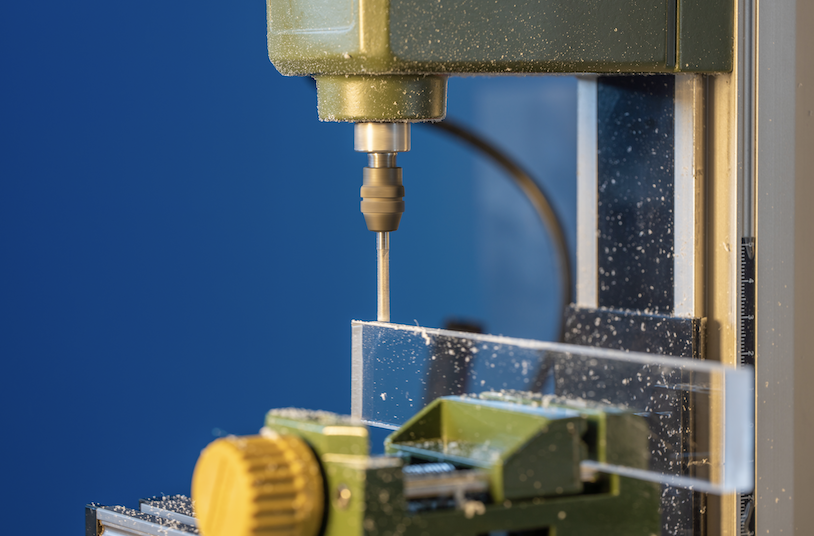
What are some common plastic fabrication methods? If your business requires custom plastic materials, you need to work with a company that provides the fabrication services required to transform raw materials into the specific form that best suits your needs. This can be done in a variety of ways. So a basic understanding of the options can go a long way toward helping you choose the right fabricator.
Custom plastic fabrication services can be useful for a huge array of companies, from transportation providers that need operator protection for vehicles to energy companies developing new equipment for sustainable power solutions. Working with a plastic fabrication specialist allows you to get the equipment you need made to your exact specifications. A vendor with the right capabilities can allow you to choose basically every aspect of your finished product, from size and thickness to shape and material. But you need to make sure that the supplier you choose has the ability to actually form raw plastic materials using quality techniques and equipment in order to reap these benefits.
There are several plastic fabrication methods available to help shape and form a variety of materials. Thermoforming and fabrication assembly are two of the most prominent and useful strategies that companies that use plastics should be aware of. Here’s a rundown of these two options so you can have a better understanding of how they might benefit your operations.
Thermoforming
Thermoforming is a plastic fabrication process that uses high heat to form the material into a specific shape. In the most basic example of this method, a plastic fabricator will start with a single sheet, which is then heated in an oven or similar mechanism to a temperature where it is able to be easily pliable. The exact temperature may vary depending on the exact type of plastic used. From there, the sheet or thin layer of plastic film is then applied over a mold that is in the shape you want for the final plastic product. So for example, if you’re having a custom windshield made, you would need a mold with a slight curve that fits over the front of the vehicle in question. From there, the plastic is cooled in place until it is no longer pliable. It can also be cut to size during this process.
Thermoforming is a very efficient and accurate method for plastic fabrication. It’s also easy to produce at scale, since there is large, industrial equipment available for exposing large volumes of plastic to high heat in order to form it accordingly. There are also smaller machines available to complete less intensive workloads.
Thermoforming is only a viable option for certain plastics that are able to be manipulated at high temperatures without breaking down. Luckily, this includes some of the most popular and versatile plastic materials available, including polycarbonate and acrylic. Basically, anytime you need a single piece of plastic formed into a curved, bent, or irregular shape, thermoforming is potentially a viable option. It can also be used in conjunction with other plastic fabrication methods, like routing.
Fabrication Assembly
Plastic fabrication methods also include plastics that can also be formed and fabricated into finished products using various assembly methods. This concept basically refers to bonding and attaching plastics together to form more complex shapes or products. The specific adhesives and assembly materials used can vary depending on the exact specifications of the project. However, the general concept allows plastic fabricators to create solutions that wouldn’t otherwise be possible using a single mold and piece of plastic material.
More specifically, plastic fabricators can use bonding and gluing, plastic welding, or even mechanical joining methods to bring multiple components together. The exact option you choose may depend on the type of plastics included in a project, size and scope of the finished product, and any other specific needs in terms of durability or maintenance. An experienced plastics fabricator can help you understand how each specific method might impact your company’s needs in various ways, and then point you toward the solution that’s the best fit.
Basically, this concept can include a variety of different techniques, used individually or alongside other methods. It’s applicable to nearly any type of plastic and any complex project where you need to bend, form, or attach plastic materials from sheets or other basic shapes. The possibilities for joining and manipulating various materials using these methods are pretty much endless. So it’s certainly a technique that you should look for when considering plastic fabrication vendors going forward.
If you’re looking for a plastic fabrication vendor that offers these capabilities, look no further than Polymershapes. We offer custom plastic materials and fabrication services for companies in a wide array of industries, including transportation, construction, energy, retail, and manufacturing. Our Dayton fabrication center is ISO 9001 certified and ITAR compliant, and we’re equipped to deliver quality products and prompt service to clients throughout the Midwest and East Coast. We use state of the art equipment to give you the highest quality materials and fabrication services available, and our team will help you customize plastics for your specific size, safety, and strength requirements. If you want a plastic fabricator that is equipped to offer top of the line services to suit your exact specifications, visit our website today. Simply request a free quote and we’ll get back to you within 24 hours to go over your needs.