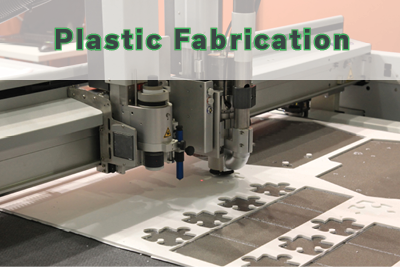
Most plastic components start off in basic shapes like sheets, rods, and tubes. These simple forms offer a good jumping off point. But most commercial, government, and industrial users require solutions that are customized to their specific industry requirements. So these materials are not usually ready for use in these stock sizes and shapes. That’s where plastic fabrication services come in.
Most plastic materials can be cut, routed, thermoformed or otherwise manipulated to create the desired end shape that works for your specific project or application. A sophisticated plastic fabrication facility should be equipped to transform raw materials into intricate parts that are ready to be installed or added to your specific applications.
If you’re in the market for high performance plastic materials and want to learn more about the customization options available, here are some of the most common options and the popular applications they’re used for.
Cutting
Cutting can be a straightforward or intricate plastic fabrication process. If you need a simple square or rectangle sheet of plastic, those materials can be saw cut to size or guillotined. Guillotine cutting involves making straight cuts on all sides. It can be done to precise measurements and can even be repeated for those that need multiple sheets of the same exact dimensions. For example, you may need simple sheets in set dimensions for signage, packaging, or other retail applications that need to fit in multiple locations.
For those businesses and organizations that need thin plastics like rolls of film, you may benefit from a process called slitting. This type of plastic fabrication involves cutting the entire roll to a specific length. Then you can continue to use the roll as needed, since it’s already cut to your exact specifications. This may be beneficial for any operations that require the ongoing ability to access films for specific purposes. For example, companies that produce ID cards can get rolls made to the width of the cards they produce so they can easily laminate them as they’re produced.
Cut-to-size plastics are certainly useful in a wide array of industries. However, specialized plastic fabrication often requires equipment with more extensive customization features. Specifically, Computerized Numeric Control (CNC) production saws can cut plastics into unique shapes based on digitally created designs. CNC machines can cut a huge array of plastics and gauges. They even work with multiple sheets stacked together to accommodate high volume production needs. And since they make cuts based on digital designs, they can easily be repeated and automated to save time. This type of plastic cutting is often employed for businesses that require precision parts, like gears or bearings for industrial facilities.
Machining
Cutting is useful for businesses that require two dimensional plastic components. However, there are many plastic applications that may benefit from additional customizations or three dimensional items, which is where the following machining techniques can come in handy.
Milling involves the use of rotary cutters to remove plastic material from a three dimensional shape. This tool can be inserted into the material from several directions and apply various levels of pressure and speed to create completely customizable shapes. This is often used to create specialized equipment for industries like mining and construction.
Turning is used to make cylindrical parts. It employs a cutting tool that moves in a straight line as the plastic rod or tube rotates on a central axis. This technique can be used for any cylindrical parts, including those in the energy, oil, and gas fields.
Thermoforming
Many plastics can also be formed into specific shapes when targeted heat is applied to the material. These are known as thermoplastics, and this category includes several popular materials like acrylic and polycarbonate. They become malleable when exposed to certain temperature ranges. But they also stiffen again when cooled. And these materials do not degrade or change their chemical structure when exposed to these temperature shifts.
There are multiple ways to apply heat and then manipulate the material to change the finished shape. Vacuum forming is one popular method. Once heat is applied, vacuum suction is applied to fit the material over a mold. Drape forming involves draping heated sheets over a mold and holding them in place until they cool down. Free blow molding uses compressed air to form plastic sheets into a dome shape. Compression forming uses two molds — one that contours to each side. Then there’s plug assist molding where an object is inserted into a plastic sheet to pre-stretch the material. All of these techniques are helpful when shaping plastics into specific parts, like machining components. They can also be used for simple shapes, like an arch for the top of a carport or awning.
In addition to these specific types of heat forming, there are bench fabrication and finishing techniques like heat strip bending, cold forming, hot stamping, edge finishing, and polishing. These are often used in addition to other techniques listed above.
No matter what type of plastic fabrication services your operations require, your local Polymershapes facility can help. We offer a huge assortment of high performance plastics from top manufacturers. And our local facilities are all outfitted with an array of plastic fabrication equipment to provide the exact components needed to support your operations. We also partner with a network of fabricators to help provide our customers access to any services we may not offer in-house. If you’re ready to learn how our plastic fabrication options can benefit your operations, visit our website to reach out to your local Polymershapes branch today.