The healthcare industry relies on precision and strict compliance for every product they commercialize. Due to these needs, the manufacturing process undergoes constant scrutiny. The primary question product engineers have to solve is how to develop new products within cost targets without reducing quality. This can only be accomplished through DFM evaluation. Manufacturability measures how effectively a product can be developed given material availability, design, costs, and ease of manufacturing.
Manufacturability has a strong correlation with product design. However, manufacturability can be difficult to measure because of the vast array of materials and processes available. Working with an experienced and reputable plastics expert can help mitigate those difficulties. Many OEMs have shifted from metals to plastics, increasing the need for medical-grade plastic. Polymershapes is one of the largest North American distributors of medical-grade plastic, with decades of experience responding to changes in compliance and manufacturability.
As OEMs embark on this major transition, figuring out which plastics would best suit each application can be a monumental feat. With Polymershapes’ relationships and experience with the world’s most reputable plastic manufacturers, we can ensure that the manufacturing process is fully streamlined as needs and material availability evolve.
What is Design for Manufacturability (DFM)?
DFM is a set of guidelines and best practices used to streamline the development and manufacturing of new products. Many sectors within the healthcare and medical industry utilize DFM to maximize production while minimizing costs, energy consumption, material waste, etc. It accounts for the entire manufacturing process, from pre-production development to the assembly process. It considers the materials, techniques, and processes used to ensure the most cost-effective solution without sacrificing quality.
Benefits of Polymershapes’ DFM Expertise
When developing and producing new products, the medical industry needs to adhere to strict specifications. Such regulations can include guidelines for traceability, sterilization, biocompatibility, and more. Polymershapes is experienced in the DFM process, with the expertise to determine:
- Most effective method of manufacture: With all the strict regulations and guidelines in place, determining the most cost-effective way to develop a product can be difficult. Polymershapes partners with industry-leading medical-grade plastic manufacturers, with years of proven experience reducing production costs and maximizing quality.
- Which material is best: Each medical application comes with its own unique needs, and there is a wide selection of plastics with their own traits and qualities. Experienced plastic specialists from Polymershapes can help refine product design to promote long-term performance and compliance.
- Access to industry-leading vendors and manufacturers: Polymershapes works closely with the most reputable names in healthcare industry plastics, including SABIC, Mitsubishi Chemical Group, Simona-Boltaron, and more.
- Preparation and risk management: Valuable insights from plastic specialists can keep you in-the-know so you can anticipate potential needs, supply issues, or other challenges. This will help ensure the most effective manufacturing process possible, regardless of market conditions. This will also prevent last-minute disruptions that will require costly recalls or redesigns.
- Reduction of material/medical waste: Any time a product needs to be redesigned to compensate for a flaw, a significant quantity of material may need to be scrapped. Designing for manufacturability can help avoid costly mistakes, reducing how much material gets wasted.
Designing for manufacturability is a crucial element of reducing costs and navigating potential risks. By assessing the current state of the market, and the challenges that may lie ahead, developing and launching new healthcare products becomes significantly less difficult.
The Cost Effectiveness of Design for Manufacturing (DFM)
The key to long-term success is balance. The goal of DFM is to strike a balance between high-quality products, manageable costs, and quick time to market. Unexpected delays, material constraints, recalls, or late-stage design fixes could all have a significant impact on overall production costs.
Polymershapes has direct insights into the state of the plastics industry. Having an experienced partner that works with healthcare plastics can help reduce the impact of market/industry fluctuations.
Sustained Innovation and Time to Market
Innovation is powered by bringing new devices and products to market. When the production process is streamlined, costs can be reduced, and newer technology can quickly drive the healthcare industry forward. Designing for manufacturability helps keep costs low and allows for new developments to work their way into the field more consistently. The result is less funds being dedicated to production costs and/or energy consumption, and more funds that can go into further research and development.
Working with a team like Polymershapes can help provide extreme flexibility. A comprehensive DFM process can incorporate a wider range of materials and allow for regular refinement. The result is a consistent stream of innovation that bridges the present to the future.
Change Notifications and Improved Adaptability Post-Launch
Change notification is the single biggest challenge product engineers face. With development and regulatory costs being so high, product engineers need to tighten up all loose ends before it comes time to launch. Otherwise, post-launch redesigns could induce all kinds of financial strain. Design changes are one of the worst-case scenarios for engineers, and working with plastics experts at Polymershapes can provide valuable insights into which materials are best. Identifying the best material upfront can improve the design process and reduce the likelihood of a redesign later.
If a redesign ever is needed, DFM allows you to have an answer upfront and reduce the downtime of reintroducing a product.
Product Consistency and Long-Term Industry Reception
In a sector that relies heavily on precision and consistency, designing for manufacturability helps achieve both. Delivering a well-developed, high-quality product not only reduces the effects of change notification or post-launch redesigns, but also reduces the chances of failure in general. Delivering a product that is properly designed and uses the right materials allows each individual unit to perform as intended. The result is a consistent and reliable product, which will leave a mark on the industry.
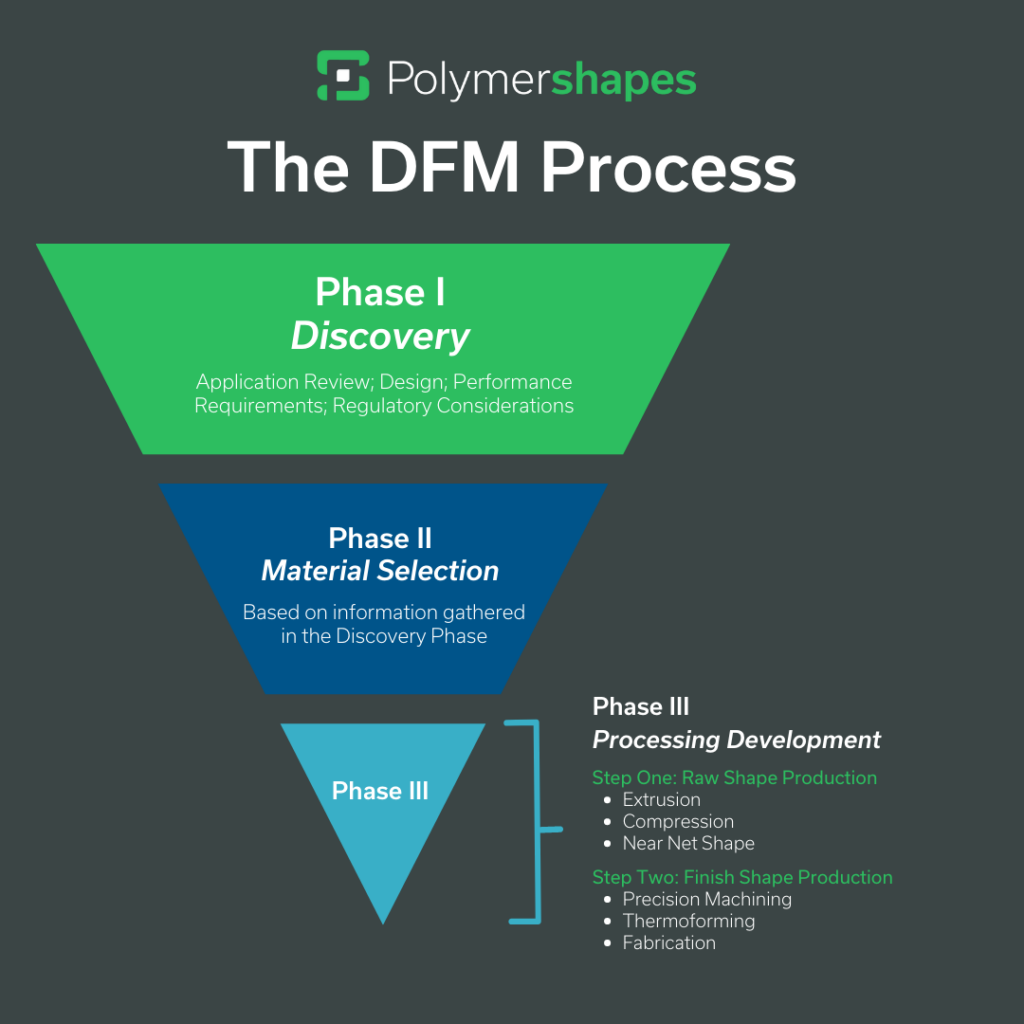
The Polymershapes DFM Checklist
Formulating a cohesive process involves an in-depth checklist that explores every depth of the manufacturing method, the product itself, and its future application. To make sure every box is checked, DFM usually investigates the following:
- Consider design regulations, compliances, application needs, material availability, and other cost-adding constraints to choose the best material and manufacturing process.
- Select the best material and process to meet part order volume and production timeline benchmarks.
- Design parts to ensure the manufacturing process can minimize waste material and reduce time spent machining or assembling.
- Review application needs, such as tolerances, sizing, function, etc. to ensure optimal part performance.
- Review the design of assembly, including number of parts, time needed to complete the process, etc.
- Upon completion of the manufacturing process, test the product’s tolerances to prepare for future inspections.
- Review proper and accurate production labeling.
- Review designs of assemblies, hardware, etc.
By scrutinizing every step of the process, implementation can be much more straightforward, and production will be far more streamlined. The result is a product that closely aligns with performance expectations and also meets BOM costing targets.
Design for Manufacturing Throughout the Process
To get the most out of a DFM plan, it must be adopted and incorporated from the very beginning. The process only works if we incorporate it from napkin to commercialization. The goal is to prevent being bogged down by the constant need to retroactively fix issues that bottlenecked production in the first place. Every single hiccup adds up and can significantly impact the overall time to market. The impact of missing design issues becomes more and more costly to fix as you get closer to commercialization.
By having a plan in place that considers all possible options before production has even begun, it becomes easier to reduce the impact of those hiccups. Also, investigating the manufacturability of a part, device, or product early in the production cycle makes it possible to create a fully streamlined and consistent process.
Polymershapes can help formulate a comprehensive DFM plan that is designed to maximize production and performance at the lowest possible cost. Our experienced specialists and reputable suppliers help OEM’s lead the charge on medical and healthcare innovation. To learn more about medical grade plastics, DFM, and how we can support your R&D efforts, contact Polymershapes today.