Fabricated plastic parts provide value in a huge array of industries. Since plastic can easily be molded, bent, cut, and otherwise manipulated into specific shapes and sizes, it is an ideal option for applications and industries that need components that fit precise dimensions.
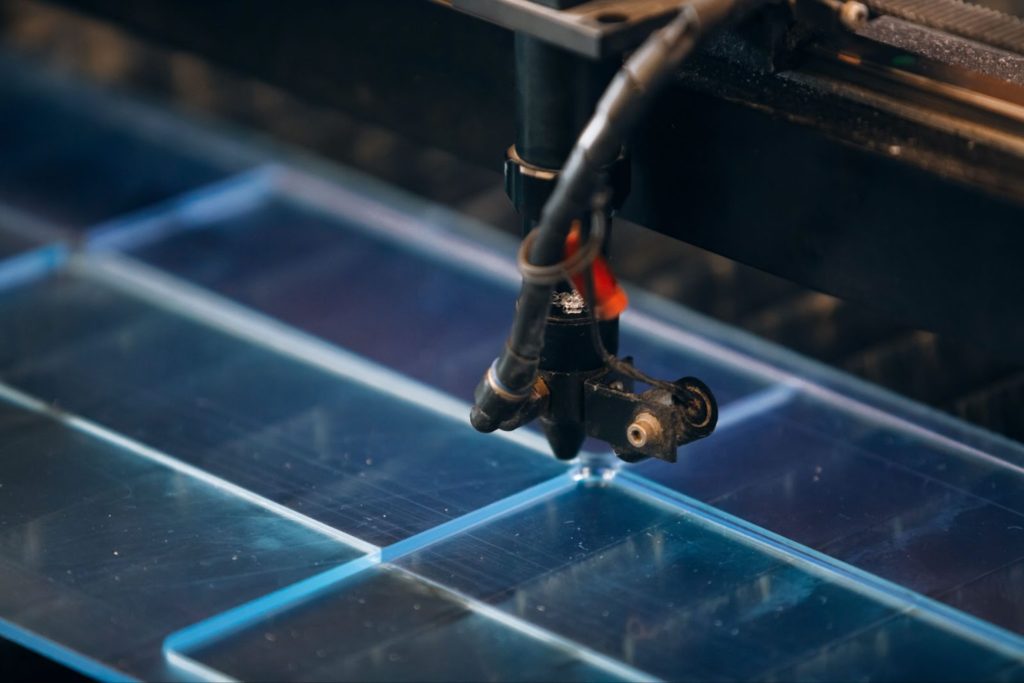
Though this practical benefit can apply to nearly every field, it is especially relevant in the production of medical device components, industrial equipment, and wear parts that fit into machinery or mechanical settings. Here’s a rundown of some of the benefits and specific uses of fabricated plastic parts within these fields.
Fabricated Plastic Parts For Medical Components
Fabricated plastic parts within the medical industry can be used in implants, prosthetics, surgical equipment, and even trays and support materials used around hospitals and doctors’ offices.
Plastics meet many of the most strict standards within this industry, including compliance with FDA and USP testing protocols, lightweight, and heat, and chemical resistance. Specifically, many materials must be able to be sterilized, either with chemical solutions or steam and extreme heat. Others, like those used in implanted devices, must meet strict biocompatibility standards to ensure patient safety.
While there are nearly endless potential applications for fabricated plastic parts within the medical industry, here are a few areas where the ability to mold and shape components to suit the needs of patients can be especially beneficial.
Orthotics and prosthetics are medical support devices that are generally customized to the shape and size needs of each patient. For example, a brace that protects and supports a child’s legs as they develop must fit that child perfectly at their particular stage of growth. They may then require slightly larger braces as they grow.
Plastics are often selected in this field not only because of their easy customizability, but also because they are incredibly comfortable and lightweight, making the experience of wearing them more pleasant for the patient. They can also mimic both the look and feel of natural parts more effectively than other materials like metal.
Plastics that are often used in the production of orthotics and prosthetics include UHMW, HDPE, LDPE, and Polypropylene, among others.
Medical instruments and sterilization trays can also be produced using fabricated plastic parts. Plastics like Polyetherimide, Polycarbonate, and Polypropylene all provide the strength, structural integrity, and durability to withstand various medical sterilization processes. For example, many sterilization trays must go through high-temperature processes like steam cleaning, while others are exposed to sterilizing chemicals.
Medical packaging is another common area where plastic materials are necessary. In these applications, there is no room for compromise in ensuring total protection. So materials must be strong, durable, and a perfect fit for the materials that they are charged with protecting.
The exact types of plastic and shapes provided change depending on the specific product. For example, some items require clamshell packaging or lidding, while others can be packed into blister packs or folding cartons. Some medical manufacturing and packaging facilities may even require multiple materials and solutions to suit their entire suite of products.
Wear Applications for Plastic Fabricated Components
Industrial facilities also tend to rely heavily on fabricated plastic parts to protect machinery components and facilitate essential processes. Again, since there are so many different types of plastics available, and since they can be molded, shaped, and cut into nearly endless shapes and sizes, the list of potential applications is quite extensive. But here are a few of the most popular use cases that industrial clients may benefit from.
Bearings and bushings are used in nearly every manufacturing facility around the world. Not only do these seemingly small wear parts provide essential cushioning to various metal components, but they can also reduce the amount of maintenance necessary to keep machinery functioning properly and prevent downtime that costs facilities money in the long run.
For these applications, users need high-quality engineered plastics like UHMW, Acetal, and PEEK, which actually can outperform metal bearings and bushings across various industries and applications due to their lightweight, chemical resistance, and ability to stand up against friction.
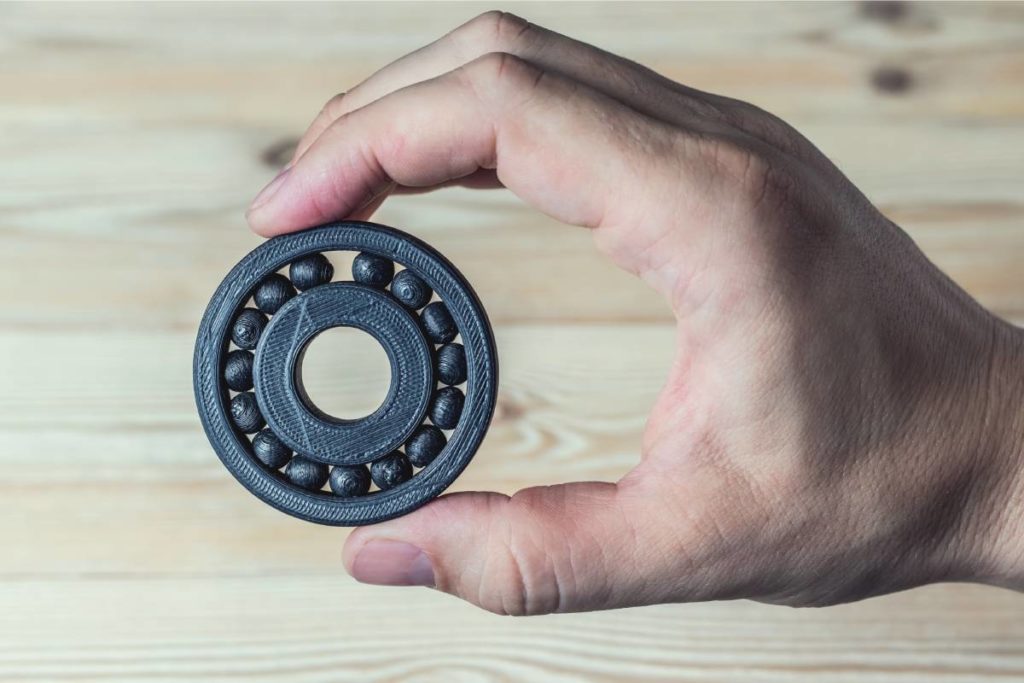
Plastic can also be superior to metal when it comes to the production of gears. Specifically, plastic offers enhanced design flexibility, since it can be molded into various shapes to fit into existing machinery. They’re also lighter and better suited to absorb noise and impact, resulting in quieter and smoother machining processes.
They also don’t require added lubrication to function properly, but they can be mixed with additives to improve performance in a particular area if needed. Many plastics even provide chemical and corrosion resistance, allowing them to outperform metal gears in wet environments.
In addition, conveyor equipment often utilizes fabricated plastic parts in machinery used to move bottles, boxes, and various other products.
Specifically, many of these machines utilize plastic wear strips along their guardrails to prevent damage to products and other machinery components. Basically, these smooth pieces of plastic that are fitted to each machine allow products to easily glide through the manufacturing floor. Plastic outperforms metal in these instances since it has a bit more give and flexibility, which prevents breakage of glass bottles or other delicate materials. This small change can even allow manufacturing facilities to move products more quickly and reduce machinery downtime.
If you’re looking for fabricated plastic parts for any of the applications listed above, Polymershapes can help. We offer a huge array of high-performance plastics and connect clients with value-added conversion and fabrication services to ensure they’re made to your exact specifications.
Our products are well suited for various applications in a huge array of industries, from data centers to medical device manufacturers and aerospace companies. Visit our website to find your nearest distribution center and reach out to our knowledgeable team to get started.